Dr.-Ing. Thiago Weber Martins
Contact
Thiago Weber Martins studied Mechanical and Process Engineering at Technische Universität Darmstadt until 2014.
During his studies he worked as a student assistant at the Department of Computer Integrated Design and supported the supervision of tutorials like „Programming Languages and Techniques (Programmiersprachen und -techniken (PST))“ and „Introduction in Computer-Aided Design (Einführung in das rechnergestützte Konstruieren (CAD))“. In addition, he supported the collaborative research cluster 666. Within the collaborative research cluster 805, he wrote his bachelor thesis on the subject of a conception of the identification and the classification of design zones affected by uncertainty.
He successfully completed internships at Federal-Mogul GmbH and Lufthansa Technik AG.
In the March of 2014 he joined the Department of Computer Integrated Design as a research assistant.
Since 2014 he is responsible for the lecture and tutorial of “Basics of CAE/CAD”. Additionally he is responsible for the lecture and practices of DiK within the CRC 666 project lectures “Innovative steel metal products – From conceptual design to final component”.
Topics: CAD/FEM, CAD/MKS, CAD/CFD, NX Open, Virtual Product Design
Collaborative Research Center 666: Integral Sheet Metal Design of Higher Branch Order – Development, Production, Evaluation
Thiago Weber Martins is member of the Collaborative Research Center 666 (CRC 666) since 2014 and works on the project A4. The Collaborative Research Center (CRC) 666 – Integral Sheet Metal Design with Higher Order Bifurcations – is running from July 2005 to June 2017. Its goals are the development of methods and techniques that support the optimized design of bifurcated integral sheet metal parts. In subproject A4 modeling capabilities for nonlinear, branched sheet metal parts are researched. In the third funding period, the focus will be on methods and tools for modeling by means of multiparametric features, which will enable a view-specific modeling of the bifurcated sheet metal parts developed in the Collaborative Research Center. The parts topology is assigned to context-dependent geometry information and supplemented by microgeometric and technological information, so that planning data for the forming by flow splitting and bend splitting can be derived. Thiago Weber Martins was also leader of the working group 2 “Nonlinear Bifurcations”. For more information about CRC 666 and TP A4, see this link.
Topics: CAD, Virtuelle Produktentwicklung, NX Open
Space Factory 4.0 – Basic development for the robotic assembly of highly modular satellites on an in-orbit platform based on industry 4.0 processes
Currently, Thiago Weber Martins is project leader of Space Factory 4.0. It is a joint project dealing with the basic development for the robotic assembly of highly modular satellites on an in-orbit platform based on „Industrie 4.0” processes. It is funded by the German Aerospace Center (Deutsches Zentrum für Luft- und Raumfahrt – DLR) and the Federal Ministry for Economic Affairs and Energy (BMWi). The Technische Universität Darmstadt, the Technische Universität München and the Zentrum für Telematik (ZfT) in Würzburg are involved in Space Factory 4.0. Furthermore, three companies from the aerospace industry, OHB System, Von Hoerner & Sulger (VH&S) and Telespazio VEGA Germany are taking part as subcontractors in this project. In scope of Space Factory 4.0, Thiago Weber Martins deals with innovative processes based on the latest findings from the introduction of Industrie 4.0 in Germany for the assembly of highly modular satellites. The approach of the Digital Twin plays a central role and is extensively explored within this project. For more information about the Space Factory 4.0 project, see this link (http://www.dik.tu-darmstadt.de/forschung_dik/projekte/aktuelleprojekte_5/space_factory_4__0/spacefactory40.en.jsp)
Topics: Industrie 4.0, Digital Twins, Space 4.0
Advanced Design Project
- Mobile user interface for the data conversion of optimized geometry data of higher branch order metal design (2015) – finished
- Integration of manufacturing information into development process (2015) – finished
- Virtual Demonstrator of Façade Cleaner (2015) – finished
- Development and Verification of a Cleaning System for the Virtual Prototype of Façade Cleaner (2016) – finished
- Advanced-Design-Project: Process chain CAD-MKS for Providing Planning Data for Flexible Splitting Processes (2017) – finished
- Advanced-Design-Project: Demonstrator for the measurement of integral sheet metal parts with higher order bifurcations (2017) – finished
- Development of a Digital Twin for the robotic assembly of small satellites based on CAx-process chains (2018)
Bachelor Thesis
- Development of Methods for the Automated Processing of Optimized Branched Structures from the XML Format to 3D-CAD Models (2015) – finished
- Investigation on the optimization potential of non-linear bifurcations in the field of line systems (2015) – finished
- Modeling approaches for CAD/CAE systems (2016) – finsihed
- Development of a feature library for the web-based application for modeling higher branched sheet metal design (2016) –finsihed
- A cloud based server for the Space Factory 4.0 (2018)
Master Thesis
- Concept for the integration of morphing boxes for shape optimization in SIMULIA TOSCA Structure and CATIA (2015) – finished
- Parametrization of optimized data for the algorithm-based modeling of manufacturing-ready CAD-models (2016) – finished
- Development and Validation of a Parameterization Method for Forming Tool Design (2016) – finished
- Computer Integrated Design of Torsional Spring for an Exoskeleton Module (2017) – finished
- Algorithms for the derivation of feature-based model history to automatic CAD model generation (2017) – finished
- A basic reference model for the geometrical instantiation of digital twins of a small satellite (2018)
- The use of Digital Twins in small satellite programmes – a reference architecture (2018)
- Conception of a Generic Method for Systematic Creation of Business Process Models for the Space (2018)
- Using the Digital Twin for Automating Test Procedures in Space (2018)
- Application of Neural Networks for Space Missions – Modelling and predicting behavior of analogue sub-systems using neural network (2018)
- Development of a Control System 4.0 – Application of Industrie 4.0 Ap-proaches for Control Systems in Context of Space Missions (2018)
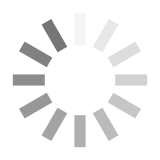
Error on loading data
An error has occured when loading publications data from TUbiblio. Please try again later.
-
; {{ creator.name.family }}, {{ creator.name.given }}{{ publication.title }}.
; {{ editor.name.family }}, {{ editor.name.given }} (eds.); ; {{ creator }} (Corporate Creator) ({{ publication.date.toString().substring(0,4) }}):
In: {{ publication.series }}, {{ publication.volume }}, In: {{ publication.book_title }}, In: {{ publication.publication }}, {{ publication.journal_volume}} ({{ publication.number }}), ppp. {{ publication.pagerange }}, {{ publication.place_of_pub }}, {{ publication.publisher }}, {{ publication.institution }}, {{ publication.event_title }}, {{ publication.event_location }}, {{ publication.event_dates }}, ISSN {{ publication.issn }}, e-ISSN {{ publication.eissn }}, ISBN {{ publication.isbn }}, DOI: {{ publication.doi.toString().replace('http://','').replace('https://','').replace('dx.doi.org/','').replace('doi.org/','').replace('doi.org','').replace("DOI: ", "").replace("doi:", "") }}, Official URL, {{ labels[publication.type]?labels[publication.type]:publication.type }}, {{ labels[publication.pub_sequence] }}, {{ labels[publication.doc_status] }} - […]