Areas of expertise
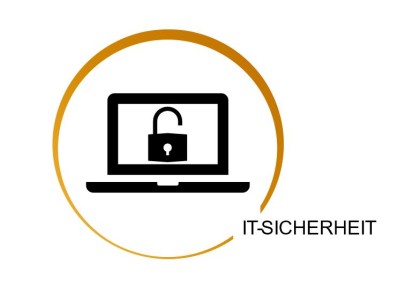
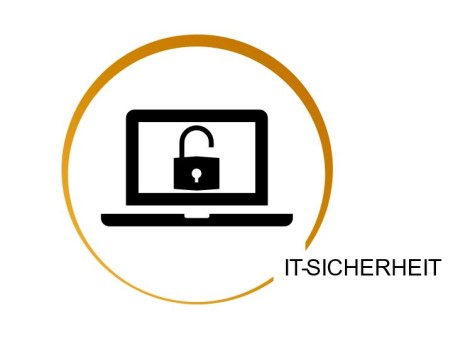
Due to the increasing networking and digital communication in the industrial environment, knowledge protection and IT-Security of the systems represent an essential basis for the competitiveness of companies. The PLCM department is researching new methods and concepts for the protection of systems in remote maintenance and the safeguarding of new business models such as the digital trading of company knowledge. This is illustrated with two demonstrators, which represent for example the trade of technology data for laser and fluid mixing processes. In this technology data marketplace, encrypted data records are made available via the web and decrypted on the authorized machine using a user license. Industrial remote maintenance is improved by adapted authentication and confidentiality protection methods with regard to vulnerability. This is illustrated by a model robot arm. Furthermore, encryption concepts for a distributed additive manufacturing are developed and integrated with a desktop manufacturing system.
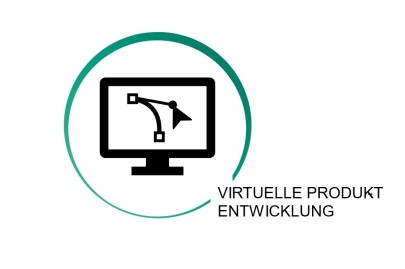

In the focus area of Virtual Product Development, the PLCM presents findings from research on digital process chains. These lead to new approaches for the development of integral sheet metal designs of higher branching orders, for the control of uncertainties in load-bearing systems and in medical technology. In addition, methods are developed to support users in the digital product development process. The demonstrators illustrate, for example, the researched approaches for the optimization of process steps in sheet metal forming on basis of algorithms. In the field of medical technology, the approaches of virtual reality and sensomotoric feedback using haptic feedback systems are demonstrated for the digital modelling of dental prostheses. These approaches make it possible to increase product quality and reduce development costs at the same time.

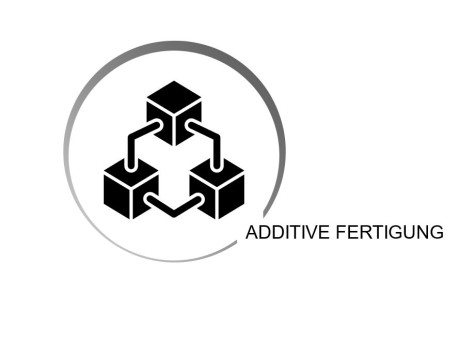
The PLCM works on solutions for the optimization and further development of additive manufacturing processes.
Additive manufacturing technologies are currently a subject to ongoing development. They are used for a wide range of tasks from creation of concept and ergonomics models, via physical prototypes up to finished parts. In this way the manufacturing technologies support the product development process. Physical prototypes, as defined by the Association of German Engineers (VDI), are used in all phases of the product development process, starting in the early stages of the design and definition to final testing of physical prototypes (VDI 3404). These application areas reaffirm the importance of the physical prototypes in the development process and thus also their integration into the virtual product development.
This ongoing development results in a comprehensive examination of the processes from the research perspective. Therefore, the digital process chain including all relevant process steps is profoundly illuminated at the PLCM. The process chain involves creating computer-based 3D-CAD models, preparation of the construction process, the physical construction process as well as the post-processing and the application of the component. Here the PLCM works on solutions for the optimization and further development of additive manufacturing processes. The solutions particularly concern issues such as the development of new exchange formats for the generative manufacturing, integration of design guidelines into the virtual design process, optimization of the Nesting process and the knowledge return from the construction process and the use phase back into the virtual product development.
The prime objective of the PLCM is to holistically optimize the depicted process chain for generative manufacturing and to integrate innovations into the process. In addition to an industrial generative manufacturing unit (Stratasys Dimension Elite / Fused Layer Modeling), there is a self-developed and constructed demonstrator in the form of a 3D desktop printer available for the implementation and validation of developed novel approaches.
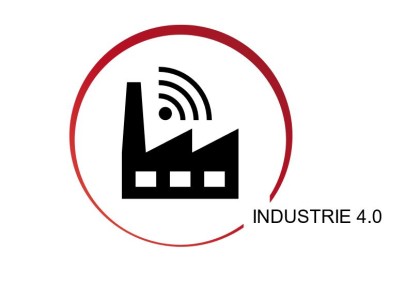

In the field of Industry 4.0, the research objective of the department is to develop methods for the combination of previously separate modelling and simulation systems. These methods form the basis for the description of digital twins. The main focus of research in this area is the use of web technologies and semantic technologies as well as the development of suitable new data management methods. The results obtained in the laboratory are validated in the model factory located at the TU Darmstadt and put into industrial practice through transfer offers.