Collaborative research
Iron as a reactive metal has enormous potential to boost the energy transition. The project Clean Circles teams up scientists from multiple disciplines to explore how the metal and its oxides can be used in a cycle as carbon-free chemical energy carrier to store wind and solar power Learn More
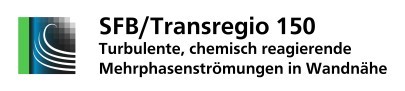
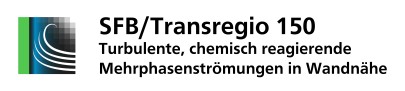
Turbulente, chemisch reagierende Mehrphasenströmungen in Wandnähe
Collaborative Research Centre/Transregio 150 associates scientists of Technische Universität Darmstadt (TUD) and the Karlsruhe Institute of Technology (KIT) with the common goal of understanding and explaining processes involved in turbulent, chemically reactive, multi-phase flows near walls. Learn more
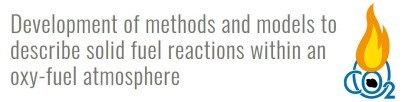
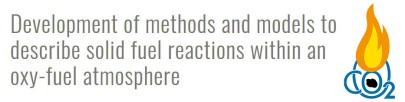
Development of Models and Methods to describe Solid Fuel Combustion in an Oxy Fuel Atmosphere
The safe supply of energy and electrical power will require operation of conventional power plants in the next decades until technical development enables the supply mainly by regenerative sources at minimum emissions of climate gases. Learn more
The Rolls-Royce University Technology Centre at TU Darmstadt was founded to investigate the aerodynamic and thermal interaction between combustion chamber and turbine. In a strategic partnership between science and industry, we develop new technologies for aircraft engines that will meet future economic and ecological goals.
Projects:
- HydrogEn combuSTion In Aero engines (HESTIA)
- Hydrogen combustion technology for new generation drive systems (WotAn)
- Investigation of turbulent mixing and flame structure in a hydrogen combustion chamber
- Particle and emission reduction technology for efficient and environmentally friendly drive systems (PERseuS)
- Development of methods for the detailed prediction of soot and NOx formation in the combustion chamber as well as virtual, cross component, modelling of interaction mechanisms between combustor and turbine.
- Consortium for the AdVent of aero-Engine Demonstration and aircraft Integration Strategy with Hydrogen (CAVENDISH)
- Cost- and performance-optimized combustion chamber turbine technologies for modern turbo generators electric aircraft engines (OptTuGen)
- Modeling of thermoacoustic instabilities in H2 combustors using hybrid CFD/CAA.
- Testability and testing of H2 drive systems and components (TeTeAnt-H2)
- Flexible Fuel Nozzle – Modeling and Simulation of Turbulent Dual Fuel Combustion (H2 and Sustainable Aviation Fuels)
In this Priority Program SPP 2419 HyCAM, a new interdisciplinary approach is being pursued that combines the competencies of combustion research and additive manufacturing. The hypothesis of the SPP is that only a comprehensive understanding of combustion fundamentals as well as the integration of modern 3D manufacturing processes through simulation-based design can enable the simultaneous improvement of flexibility, efficiency and emissions in thermochemical energy conversion processes.
Projects:
- Interaction of hydrogen flames and smart effusion-cooled gas turbine combustor walls Learn more
- Mesoscale burner array for hydrogen-rich fuels – achieving high power density, fuel flexibility, and low emissions through additive manufacturing Learn more
Internal combustion engines, in particular gasoline engines, operate with cyclic variations. Cyclic variability has been observed since the earliest scientific studies on internal combustion engines in terms of the changes in easily measurable operating parameters, such as the maximum cylinder pressure, from one cycle to another. In extreme cases, these variations can lead to misfires or knocking combustions, and in supercharged engines under certain conditions also to so-called mega-knock. Cyclic variations and the resulting unstable combustion are the major limitations for further efficiency improvements in highly optimized gasoline engines. Better understanding and modeling of the underlying physical-chemical processes offer the potential to achieve significant improvements in terms of stability, efficiency and emissions. Learn more
In NHR4CES (National High Performance Computing Center for Computational Engineering Science), TU Darmstadt and RWTH Aachen University join forces to combine their strengths in HPC applications, algorithms and methods, and the efficient use of HPC hardware. The goal is to create an ecosystem combining best practices of HPC and research data management to address questions that are of central importance for technical developments in economy and society.
INNO4SCALE is a European initiative, which was started to support the development of innovative algorithms for exascale supercomputers, so their efficient use can be fully exploited. Currently existing codes for high-performance computing will not be able to function efficiently on upcoming exascale systems in the future. Therefore, the project will identify and support the development of applications that have the potential to fully exploit the new upcoming EuroHPC exascale systems. The most successful application will be taken up by science and industry after the project.
National Research Data Infrastructure for Engineering Sciences
NFDI4Ing unites engineering research communities and promotes the management of their research data. The consortium represents researchers from every engineering field. It offers a unique method-orientated and user-centred approach to making research data FAIR – findable, accessible, interoperable and reusable.
The Task Area “Alex” (bespoke experiments) focuses on the challenges that engineers face when developing and performing a one-of-a-kind experiment to study a technical system. The experiment can be real or virtual and encompasses bespoke software and hardware solutions.
- CFD4H2 – Hydrogen direct injection for efficient monovalent hydrogen engines – experiments and 3D CFD simulations
- Experimental and numerical investigation of H2 mixture formation and combustion
- Experimental/Numerical Benchmark-Platform for scale resolving simulations with focus on ignition and early flame propagation Learn more
- Preferential evaporation of alternative fuel mixtures
- Forced ignition in turbulent mixtures of sufficiently large Lewis numbers
- CliNeR-ECo: Evaluation of multi-fuel retrofit solutions for climate-neutral e-methanol and ammonia in large maritime engines Learn more
- Center of Excellence in Combustion (CoEC) Learn more
- Green hydrogen blends – gas fuel mixtures with green hydrogen
- Understanding and modeling CO emissions (ZuKKerBroT)
- Mixture formation and combustion of alcohols and other biogenic fuels in mixing controlled combustion processes
- Development of chemical mechanisms for the energetic use of biofuels
- Formation of soot particles and catalytic filter regeneration in the engine use of gasoline from biomass
- Mixture formation behavior of bioethanol-containing fuels under diesel-relevant conditions
- Renewable low-emission fuels (E2Fuels): Research on production and utilization in a sector-coupled approach. Subproject: Modeling the ignition and combustion of OME spray flames
- Curvature effects in laminar and turbulent non-premixed combustion
- Multi Regime combustion under technically relevant conditions: Experimental and numerical investigation of thermo-chemical states and flame structures
- Multi-Dimensional Flamelet Modelling for the LES of Pulverised Coal Flames
- Engine evaporation of complex fuel mixtures with biogenic components
- CFD particle emission analysis of highly transient engine behavior
- Sustainable mobility through synthetic fuels (NAMOSYN): Numerical investigation of soot formation
- Development of a validated and efficient numerical method to extend the operating range of centrifugal pumps for pumping gas-laden liquids
- Emissions SooT ModEl (ESTiMatE)
- Innovative commercial vehicle diesel combustion process design using 3D printing processes
- CFD simulation of thermo-acoustic vibrations with compressible methods
- LowEmissionDesign LED
- ECOFLEX-turbo load- and fuel-flexible combustion (LaBreVer): Modeling and reduction of thermoacoustic sensitivity in staged lean injectors based on flame transfer functions
- Analysis of multi-stage lean gas combustion
Industry partnerships
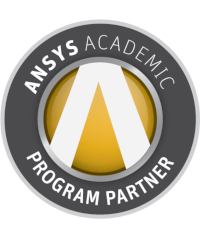
Since 2012 (as chair NTFD at TU Bergakademie Freiberg, now as STFS at TU Darmstadt) we are an official ANSYS Academic Partner. This includes access to Ansys Software and a collaboration with a focus on highly resolved simulations.
If you are interested in these topics and would like to join our young and dynamic team, we are looking forward for your application. Please either go to the application page Open Position or send your application documents directly to Prof. Dr.-Ing. Christian Hasse.